Бизнес план по управлению запасами
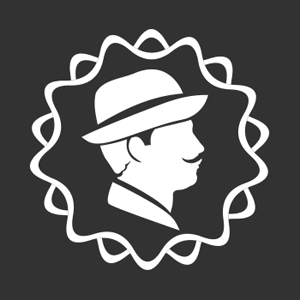
Контроль над материальными запасами
Многие предприятия игнорируют важнейшую роль, которую тщательное управление запасами играет в обеспечении прибыльности компании. Количество денежных средств, вложенных в материальные запасы или готовые товары на складе, непосредственно влияет на практические результаты деятельности компании. Каждая коробка с комплектующими не просто занимает место на складе; это разбросанные вокруг вас деньги, начальная ценность которых ежедневно уменьшается.
Конечно, достаточность запасов в некоторых ситуациях является условием успешных продаж. Каждое предприятие опасается лишиться прибыльных заказов в случае проблем с запасами, тем более что тогда вы рискуете не только объемом продаж, но и потребителями. Подобные риски возникают, когда материальные запасы компании находятся на слишком низком уровне.
Решение проблемы состоит в создании эффективного управления запасами, что приводит к существенному увеличению потоков информации между торговыми точками, производством и командой по закупкам. Данная информация позволяет добиться снижения уровня неопределенности в том, что касается необходимости поддерживать запасы. Вы должны ежедневно получать данные о том, как идут продажи товаров компании.
Вам могут помочь и поставщики. Проанализируйте вместе с ними возможности сокращения периода времени, необходимого для получения сырья и комплектующих, изучите возможность снижения объема минимальных заказов. Крупные предприятия обычно поддерживают тесные связи со своими поставщиками. Однако и небольшие фирмы должны искать поставщиков, способных обеспечить гибкость заказов и поставок.
Данный текст является ознакомительным фрагментом.
Читайте также
9.3. Управление материальными запасами предприятий
9.3. Управление материальными запасами предприятий
Наличие материальных запасов позволяет предприятию обеспечивать устойчивость ассортимента товаров, осуществлять определенную ценовую политику, повышать уровень обслуживания покупателей. Все это требует поддержания
14.2. Традиционный подход к управлению материальными потоками на предприятии
14.2. Традиционный подход к управлению материальными потоками на предприятии
Функция организации состоит в установлении постоянных и временных взаимоотношений между всеми подразделениями, определении порядка и условий производственного или торгового процесса. Процесс
14.3. Логистический подход к управлению материальными потоками на предприятии
14.3. Логистический подход к управлению материальными потоками на предприятии
При логистическом подходе управляющие воздействия к отдельным фазам движения материального потока прилагаются со стороны единой логистической системы управления. Эти управляющие
Управление запасами
Управление запасами
Регулирование запасовУровень запасовОперации управления запасами включают:– накопление и обновление данных для прогнозов;– выбор параметров прогноза;– выбор техники прогнозирования;– анализ прогнозов и моделирование;– определение целевого
6. 2. Управление запасами
6. 2. Управление запасами
Управление запасами в логистике – оптимизация операций, непосредственно связанных с переработкой и оформлением грузов и координацией со службами закупок и продаж, расчет оптимального количества складов и места их расположения. Создание запасов
6. 5. Системы управления запасами
6. 5. Системы управления запасами
Учитывая значение запасов, исследование логистической системы должно строиться на следующих вопросах:• какой уровень запасов необходимо иметь для обеспечения требуемого уровня обслуживания потребителя;• в чем состоит компромисс между
План по управлению запасами
План по управлению запасами
Успех Dell в увеличении оборота запасов состоялся не только благодаря ее стратегии прямых продаж или партнерству с поставщиками, хотя оба эти обстоятельства играют в нем значительную роль. Этот успех также – отражение товарного плана. В
«Двухъярусное» управление запасами
«Двухъярусное» управление запасами
Большинство поставщиков Dell устроили склады комплектующих около заводов Dell. Производственные предприятия расположены в Остине и пригородах Нэшвилла (США), Лимерика (Ирландия) и Пенанга (Малайзия). Каждое из этих предприятий производит
Операции с материальными ценностями
Операции с материальными ценностями
Как известно, бухгалтер работает не только с денежными средствами – как наличными, так и безналичными. На бухгалтерии лежит также обязанность учитывать все товарно-материальные ценности, принадлежащие предприятию: сырье, материалы,
Методы управления запасами
Методы управления запасами
Один из подходов к управлению запасами заключается в организации поставок по методу «точно вовремя». В соответствии с ним материальные запасы компании поддерживаются на уровне, необходимом для производства товаров по уже полученным заказам.
Управление товарными запасами
Управление товарными запасами
Основные способы учета и контроля товарных запасов следующие:• оперативный контроль остатков товаров;• инвентаризация;• балансовый метод.Повседневный учет товарных запасов осуществляется методами бухгалтерского учета. Оперативный
Вопрос 59 Анализ состояния и обеспеченности организации материальными ресурсами
Вопрос 59
Анализ состояния и обеспеченности организации материальными ресурсами
Цель анализа – выявление резервов повышения эффективности использования материальных ресурсов.Задачи анализа состояния и использования материальных ресурсов:• определить
Наблюдайте за материальными вещами
Наблюдайте за материальными вещами
Хотя я и не пытаюсь расшифровывать значения всевозможных выражений лица и движений тела, но никогда не пренебрегаю осязаемыми, физическими доказательствами. Я верю, что и вы сможете выводить некоторые ценные заключения об отношении
Источник
Правильное управление запасами позволяет поддерживать производственный процесс и своевременно обеспечивать нужды потребителей. В итоге при верной политике компания сможет извлекать максимальную прибыль.
Как эффективно управлять запасами для получения максимальной прибыли от удовлетворения спроса клиентов?
Цели и задачи политики управления запасами
Основная цель управления запасами – обеспечение производственных процессов и снижение сопутствующих затрат. Конечной целью является извлечение прибыли, обеспечение стабильности работы. Рассмотрим задачи политики:
- Установление точного объема запасов, имеющихся на складе на данный момент.
- Установление объема запасов, который нужно закупить в ближайшее время.
- Определение оптимальных сроков исполнения заказов.
Под управлением понимается расчет норм запаса, контроль над фактическими объемами, своевременное пополнение запасов. Налаженная политика необходима для достижения следующих конкурентных преимуществ:
- Уменьшение трат, возникающих вследствие недостатка сырья.
- Сокращение излишек ТМЦ.
- Повышение скорости оборота.
- Уменьшение затрат компании на хранение ТМЦ.
- Оптимизация налогообложения.
- Сокращение потерь, возникающих вследствие порчи или износа резервов.
С 2021 г. на бухгалтерскую (финансовую) отчетность в обязательном порядке станет распространяться Федеральный стандарт бухгалтерского учета (ФСБУ) 5/2019 «Запасы». Для правильного понимания новых нормативных требований, которые необходимо адаптировать к учетным системам уже сейчас, нужно проанализировать те изменения, которые носят концептуальный, системообразующий характер.
Посмотреть анализ
Рассмотрим пример. Пищевое предприятие занимается производством колбасы. Ингредиенты для ее производства хранятся на складе. Если запасов будет недостаточно, процесс производства будет приостановлен. Из-за этого потребители колбасы не получат тот продукт, который они желают приобрести. Следовательно, предприятие не сможет извлечь прибыль от реализации. Однако избыток запасов не менее опасен, чем недостаток. Если ингредиентов будет слишком много, их не удастся пустить в производство в полном объеме. Часть запасов будет испорчена в связи с истечением срока годности. Следовательно, фирма понесет убыток.
Порядок управления запасами
Управление запасами – это особая процедура, предполагающая следующий алгоритм:
- Анализ объема запасов за предыдущий период. В ходе этого этапа устанавливается действительно нужный объем снабжения. Также определяется эффективность его использования.
- Определяются цели использования резервов. К примеру, это может быть максимальное обеспечение производства в текущий момент, установление размера снабжения в сезонный период.
- Оптимизация объема запасов для обеспечения основного производства. То есть находится тот размер, который действительно необходим.
К сведению! В рамках процедуры нужно пройти каждый из этапов. Оптимизация объема невозможна без предварительного анализа производства.
Управление оптимальным размеров запасов
Неверно выполненная оптимизация может привести к этим негативным моментам:
- Недостаток средств для обеспечения производства, находящихся в обороте.
- Нарушение нормального функционирования складских помещений.
- Претензии со стороны заказчиков и потребителей.
- Истечение срока годности продукции.
Какие существуют способы пополнения оборотных средств?
В каждом предприятии имеется страховой резерв. К примеру, для нормального производства нужно 1000 единиц. Однако на складе хранится 1050 единиц. Дополнительные 50 штук нужны для использования в критической ситуации. К примеру, произошло резкое повышение спроса на продукцию. В этом случае для удовлетворения спроса потребителей будет задействован страховой резерв.
При определении оптимального объема нужно руководствоваться этими критериями:
- Ценовая политика производителя.
- Особенности закупки и реализации продукции.
- Внешние факторы. В частности, конкуренция.
Нельзя допускать переизбытка запасов. Это может привести к следующим негативным последствиям:
- Повышению расходов на хранение.
- Увеличению имущественного налога.
- Риску неполучения дохода на излишках продукции.
- Истечению срока годности.
Дефицит продукции, в свою очередь, влечет за собой эти последствия:
- Приостановку процесса производства.
- Сокращение размеров реализации.
- Необходимость в срочной закупке дополнительного сырья на невыгодных условиях.
Главное последствие неправильной политики – это появление упущенной прибыли у предприятия.
Анализ данных
Оптимизация включает в себя анализ данных. Процедура эта объединяет следующие шаги:
- Анализ настоящего спроса. Если потребители закупают в магазине 50 единиц товара, бессмысленно приобретать 200 единиц. Поэтому нужно точно проанализировать уровень текущего спроса на продукцию. На основе выполненного анализа предприятие сможет закупать именно то число запасов, которое получится продать до будущей закупки.
- Расчет страхового запаса. В рамках расчета нужно учесть все факторы, влияющие на реализацию. К примеру, это может быть сезонный спрос, поведение потребителей. Например, в среднем потребители закупают 1000 единиц продукции в месяц. Это средняя планка. Однако в теории спрос может подняться до 1200 единиц. Оптимальный страховой запас составит 200 единиц. Расчет может выполняться на основании этих стратегий: увеличение прибыли, уменьшение объема закупок, снижение затрат на хранение, удовлетворение нужд потребителей.
- Анализ излишков и дефицита. В ходе этой процедуры устанавливается текущее положение. К примеру, представители предприятия могут совершать системную ошибку: закупку избыточного объема продукции. Анализ обеспечит уменьшение вероятных рисков.
- Оптимизация товарной линейки. Определяются товары с хаотичным или стабильным спросом.
- Управленческая отчетность. Вся информация поставляется руководству в форме отчетности. Своевременное определение отрицательных тенденций позволяет быстро стабилизировать производство, не допуская существенных убытков.
Именно на основании собранной информации осуществляется управление запасами.
Стратегии управления формированием запасов
Существуют эти стратегии управления:
- Консервативная. Предприятие запасается большим объемом страховых резервов. Они нужны в случае сбоев поставок, увеличения спроса. К примеру, не удалось договориться с поставщиком о закупке сырья. В этом случае можно в течение какого-то времени пользоваться страховым резервом. Консервативная стратегия уменьшает вероятные риски.
- Умеренная. Закупаются страховые резервы на случай сбоев производства. Стратегия подразумевает средние риски и среднюю рентабельность.
- Агрессивная. Резервы максимально сокращаются. Нужно это для предельной минимизации сопутствующих трат. В этом случае предприятие будет нести минимальные расходы. Однако в случае сбоев компания понесет убытки.
Не существует оптимальной стратегии. Подбирается она на основании конкретной специфики деятельности предприятия.
Модели управления
Выделяют множество моделей управления. Рассмотрим самые распространенные:
- Модель Уилсона. Является основной. Подходит для расчета нужного объема запасов, оптимизации товара. Траты на запасы делятся на две категории: стоимость партии товара и расходы на хранение. При минимизации трат на запасы можно направить средства на хранение.
- Модель ABC. В рамках этой модели осуществляется объемно-стоимостный анализ. Резервы подразделяются на три группы. Группы формируются исходя из этих категорий: стоимость, объем, частота пользования. Группа «А» – это дорогостоящая продукция с длительным циклом пользования. Группа «В» – это запасы, которые меньше воздействуют на непрерывное производство. Группа «С» – это продукция с низкой стоимостью, которая не влияет на окончательный финансовый результат.
- Модель MRP. Представляет собой компьютерную систему со следующими функциями: обработка заказа, создание графика запасов.
- Модель установленного уровня. Новые закупки осуществляются только при достижении определенного порога запасов. Порог этот определяется самой компанией.
Модель определяется в зависимости от конкретной ситуации.
Методы оценки стоимости
Выделяют эти методы оценки:
- LIFO. Сначала в производстве используются те запасы, которые пришли последними. Метод позволяет снизить налог и уменьшить колебания цикла.
- FIFO. Сначала в производство поступает сырье, полученное ранее. Этот метод отличается существенным минусом – прямое влияние хозяйственного процесса на уровень прибыли.
- Метод средней цены. Стоимость резервов определяется исходя из средней стоимости в начале производственного периода.
- Метод наименьшей цены. Является консервативным методом. Подходит для продукции, для которой характерны колебания в стоимости.
Подбирать следует тот метод, который позволяет извлечь максимум прибыли при минимуме налоговых расходов.
Источник
Как и для большинства других хозяйствующих субъектов, основная цель для производственных предприятий — заработать деньги. Выделим основные параметры, которые будут характеризовать степень успешности предприятия на пути к обозначенной цели.
· Оборот — частота, с которой предприятие генерирует деньги путем реализации продукции, и объем соответствующей реализации.
· Запасы — это деньги, расходуемые системой на объекты, которые система намеревается превратить в пропускную способность. Величина оборота — не главный показатель хорошо работающего предприятия. Важно определить, во что организации обходится генерация этих денег, т. е. оценить возврат инвестиций. Размер оборота нельзя будет считать удовлетворительным при низком возврате инвестиций, т. е. при большом количестве запасов, или денег, которые тонут в системе. Таким образом, запасы — это не только реальные накопленные объемы материалов, комплектующих, незавершенного производства или готовой продукции, но и «квазизапасы» (здания, сооружения, оборудование, некоторые категории персонала). Впрочем, для улучшения производственных операций основное внимание уделяется именно реальным запасам.
· Операционные расходы — это все деньги, которые система тратит для трансформации запасов в пропускную способность. Сюда относятся все расходы, которые бухгалтерия считает постоянными, а также большинство переменных расходов, таких, как зарплата производственных рабочих и т. п. Чтобы быть прибыльным, предприятие должно генерировать такую пропускную способность, которая покроет все операционные расходы.
Для максимизации дохода при такой модели требуется одновременная оптимизация по трем указанным параметрам, а именно: увеличение оборота; уменьшение операционных расходов; уменьшение запасов.
Промышленное предприятие может добиться этого путем:
· возможно лучшего удовлетворения внешнего спроса по срокам, объемам и качеству (фактор увеличения оборота);
· сокращения сроков производства (фактор увеличения оборота, уменьшения запасов, в частности незавершенного производства);
· сокращения запасов материалов, комплектующих, незавершенного производства, готовой продукции (фактор запасов);
· уменьшения операционных расходов, т. е. сокращения прямых и косвенных затрат (фактор операционных расходов).
Достигнуть этого можно, выбрав оптимальный метод (и соответствующую информационную систему) производственного планирования и управления. Рассмотрим различные методы планирования для промышленных предприятий, останавливаясь на их достоинствах и недостатках.
Управление по точке заказа
При использовании метода планирования и управления по точке заказа (встречается также вариант «по точке перезаказа») предприятие формирует задание поставщикам, если объем его запасов опускается до некоего предопределенного минимального уровня. Такой метод управления больше подходит для крупно- и среднесерийного поточного производства.
Главное достоинство метода — его предельная простота. Планирование и управление по точке заказа можно использовать для управления запасами категории С (по классификации АВС), т. е. сравнительно недорогими изделиями или материалами. Недостаток метода состоит в недостаточной гибкости — в условиях позаказной работы и часто изменяющегося спроса управление по точке заказа не дает удовлетворительных результатов.
Рис. 1. Схема планирования по точке перезаказа.
В отечественной практике управления этот метод (управление по точке перезаказа) также используется при управлении производством по межоперационным заделам.
Метод Канбан
При определенных условиях (наличие партнерских отношений с поставщиками и клиентами, серийное производство и организация производственных линий, низкая стоимость переналадки оборудования для уменьшения размера производимой партии и т. д.) отличные результаты может давать метод Toyota, или Канбан. В настоящее время этот метод управления производством и запасами широко используется в Японии, Европе и США. Он является частью методологии управления «точно вовремя» (just-in-time, JIT). Сущность метода состоит в использовании простых физических сигналов (карточек, пустых контейнеров или световых сигналов), по которым производится отпуск материалов со склада, запуск производства, отгрузка потребителю.
Основная идея метода Канбан очень проста. Представьте себе некомпьютеризированный рабочий участок, на котором необходимые для производства детали хранятся в двух контейнерах. Когда один из контейнеров становится пуст, детали начинают поставляться из второго контейнера. В это время пустой контейнер подлежит новому заполнению. Таким образом, факт наличия пустого контейнера в производственной зоне — это сигнал к началу пополнения запаса. Отличие от «компьютерного» управления по точке перезаказа заключается в том, что минимальный уровень запаса определяется не компьютером, а визуально, кладовщиком (мастером) цеха или склада. Именно этот сотрудник контролирует наличие пустых контейнеров и заменяет их на полные, перемещая пустые в зону пополнения (на предыдущий рабочий участок, склад материалов, либо поставщику).
Вместо контейнеров могут перемещаться карточки, которые также будут служить сигналом к пополнению объема. Количественные меры при этом могут определяться либо емкостью контейнера, либо информацией на карточке. В зависимости от динамики спроса количество контейнеров (карточек) может быть увеличено.
Метод MRP
Метод MRP (Material Requirements Planning — планирование потребностей в материалах) предусматривает ряд стандартных шагов.
На первом этапе делается расчет нетто-потребностей в материалах на основании данных о составе изделия (спецификации). Число необходимых материалов, узлов и компонентов оценивается с учетом имеющегося в наличии или в незавершенном производстве.
Второй шаг — расчет во времени нетто-потребностей в материалах на основании данных о составе изделия. На этом этапе необходимые количества рассчитываются с учетом всех приходов и расходов материалов. Если при этом система выявляет снижение уровня материала ниже определенного уровня, то определяется количество, которое нужно закупить или произвести для удовлетворения потребности. Также возможен расчет нетто-потребностей с учетом правила партии (с учетом минимальной партии заказа, кратности партии, периодичности заказа).
Третий шаг — определение сроков закупки и изготовления. На этом этапе для отделов планирования и снабжения система определяет сроки начала действий по реализации рассчитанных нетто-потребностей. Алгоритм MRP берет за начало дату реализации конечной потребности и «раскручивает» назад во времени процесс изготовления изделия или закупки материалов, определяя даты начала производственных операций с компонентами (деталями) нижнего уровня, вплоть до определения дат формирования заказов поставщикам.
Алгоритм расчета проиллюстрирован на рис 2.
Рис. 2. Схема планирования MRP II.
Одной из особенностей метода (по сравнению с управлением по точке перезаказа) является то, что MRP не предполагает возможности отсутствия необходимых материалов на складе. Если все исходные данные и процедуры планирования выполнены корректно и все отклонения в выполнении плана учитываются своевременно, то все поставки деталей и материалов должны быть реализованы точно вовремя. Кроме того, метод MRP не «смотрит» в прошлое: необходимые материалы рассчитываются на основе информации о будущих потребностях и ожидаемых уровнях запасов на складах.
Достоинства данного метода — в возможности учитывать будущие потребности предприятия, формировать заказы на пополнение запасов в нужные сроки и в нужных объемах. Недостаток MRP — невозможность учесть ограниченность ресурсов предприятия.
Управление по схеме MRP II
Наиболее широко используемый в настоящее время метод управления производством и запасами — планирование производственных ресурсов (Manufacturing Resource Planning, MRP II). Соответствующий алгоритм включает следующие шаги.
Определяется потребность в готовой продукции, при этом учитываются все параметры спроса, а именно:
· заказы клиентов;
· прогноз спроса;
· заявки для пополнения отдаленных баз и дистрибьюторских складов;
· прогнозируемая потребность в запасных частях и т. д.
На основе этой информации формируется основной производственный план (ОПП). Алгоритм расчета плана нетривиален и очень сильно зависит от того, каким образом происходит удовлетворение внешнего спроса — путем производства на склад/под заказ, сборки под заказ или разработки под заказ.
С учетом информации по ОПП и при наличии спецификаций изделия определяются брутто-потребности на материалы, комплектующие и промежуточные сборки.
При наличии информации о запасах (незавершенное производство, запасы материалов и комплектующих, материалы в пути) определяются нетто-потребности на производимые и закупаемые части в количестве и во времени.
С учетом технологических маршрутов (с указанием пооперационной трудоемкости и норм выработки), а также информации о графике работы оборудования и выполняемых производственных заданиях вычисляется загрузка производства. При необходимости (например, в случае обнаружения перегрузки) производится перепланирование.
К достоинствам этого метода, безусловно, следует отнести возможность получения очень точных планов закупок и производства.При этом методика планирования (в случае ее корректного использования на предприятии) будет превосходно работать даже при нестабильных внутренних и внешних условиях. К примеру, можно компенсировать такие факторы, как срывы поставок материалов и комплектующих (по срокам и количеству), нестабильно работающее оборудование, изменение внешнего спроса (скажем, отказ клиента от заказа). Благодаря простому алгоритму метод управления запасами и производством MRP II в настоящее время используется большинством западных предприятий; постоянно растет число его приверженцев и среди российских менеджеров.
Недостаток метода заключается в его относительной сложности. Сама логика построения алгоритма MRP II основана на проведении множества вычислений, что означает необходимость развитой информационной системы класса MRP II или ERP. Кроме того, весьма высокие требования предъявляются к точности информации о состоянии предприятия, поставляемой в систему. Так, количество имеющихся запасов должно оцениваться с точностью не менее 95%, такая же точность требуется при планировании производственных заданий и заказов поставщикам, при определении спецификаций и технологических маршрутов и т. д.
Отметим, что сложность и требовательность характерны для всех высокотехнологичных современных методов управления. Так или иначе, если предприятие стремится вывести свое производство на мировой уровень, требование к наличию информационной системы и точности информации в ней должно быть безусловно выполнено.
Среди недостатков метода, ограничивающих его применение на многих российских промышленных предприятиях (особенно в компаниях, выпускающих сложные изделия с множеством уровней вложенности, компонентов, операций и т. д.), следует также назвать планирование без одновременного учета мощности, планирование в прошлое (без «учета сегодня»), невозможность надежно связать потребность нижнего уровня с «родительской» потребностью.
Управление по узким местам или критическим ресурсам
Метод управления по узким местам чрезвычайно эффективен для предприятий, имеющих ярко выраженные критические ресурсы, т. е. объекты управления, ограничивающие объем выпуска. Под критическими ресурсами в данной методологии понимаются как средства производства, скажем рабочие участки или единицы оборудования, высококвалифицированные рабочие и т. п., так и процедуры управления.
Основной принцип управления по узким местам состоит в том, что для улучшения работы всего предприятия нет необходимости детально управлять всем производством — достаточно сосредоточиться только на критических ресурсах, оптимизируя их, пока они не перестанут быть узкими местами. Сложность обычно заключается в определении этих критических ресурсов, ведь таковыми могут быть не конкретное оборудование, а процедуры управления, например планирования.
Метод управления критическим ресурсом получил название «барабан — буфер — веревка». Ритм работы всей системы (предприятия) должен определяться ритмом работы и объемом производства узкого места (барабан). В применении к машиностроительному предприятию это означает, что любой рабочий участок должен производить ровно столько (не больше!), сколько может переработать критический ресурс. На российских промышленных предприятиях это правило нарушается чаще всего в случаях, когда заработная плата рабочего персонала зависит от выработки. В этом случае они заинтересованы в производстве как можно большего количества изделий, вне зависимости от пропускной способности критического ресурса. Такая политика ведет к увеличению уровня незавершенного производства, что в свою очередь ведет к увеличению времени производства.
Далее, перед критическим ресурсом создается страховой задел (буфер), призванный в любых условиях обеспечить узкое место работой, повысить степень утилизации ресурса. Поток работы, поступающий на вход системы (начальные участки производства), регулируется состоянием критического ресурса (веревка).
Итак, критические ресурсы являются объектами, ограничивающими весь оборот системы, поэтому значительное внимание при этом уделяется определению узких мест, работе с ними и их устранению.
Рекомендации здесь следующие:
1. Определите критический ресурс.
2. Определите метод наиболее эффективного использования ресурса (создайте буфер).
3. Подчините все другие ресурсы узкому месту (барабан).
4. Устраните узкое место.
5. Не позволяйте инерции стать, в свою очередь, ограничивающим фактором (процедуры работы с этим узким местом).
Главное достоинство этого метода — возможность получения результата в кратчайшие сроки. Основной недостаток состоит в том, что для некоторых типов производств (как правило, это уникальные производства) критические ресурсы непостоянны. Заметим, что такое на практике встречается крайне редко.
Метод управления по критическим ресурсам, получивший также название ОТП (оптимизированная технология производства), очень часто используется в рамках систем класса MRP II и ERP наряду с одноименными методами.
APS: синхронное планирование
Методика усовершенствованного, или синхронного, планирования (Advanced Planning and Scheduling, APS) — одно из новейших достижений западной мысли в области управления производством и запасами. Считается, что именно эта методика, появление которой датируется примерно 1995 годом, со временем вытеснит из обихода метод управления MRP II. Справедливости ради необходимо отметить, что это в основном применимо для предприятий, ориентированных на удовлетворение внешнего спроса под заказ.
Структурно указанный метод может быть разделен на две части — первая связана с планированием производства и снабжения, вторая — с диспетчеризацией производства. Алгоритм работы первой части схож с алгоритмом работы MRP II. Существует, однако, небольшое, но существенное различие. Планирование по алгоритму MRP II, как мы уже упоминали, выполняется по рекурсивной схеме: 1) планируется закупка или производство необходимых изделий из расчета бесконечных ресурсов; 2) оцениваются ресурсы; 3) в случае несоответствия доступной мощности ресурса и планируемой загрузки производится перепланирование даты запуска в производство с учетом конечной мощности; 4) затем, поскольку даты изменились, производится перепланирование закупки или производства, опять же из расчета бесконечных ресурсов; 5) далее повторяются шаги 2, 3 и т. д.
Такой процесс занимает значительное время, поэтому, как правило, не может производиться постоянно (на ежедневной или даже на еженедельной основе). В промежутках между перепланированием никак или почти никак не учитываются отклонения от плана, которые в производстве могут происходить достаточно часто. Этим обстоятельством можно пренебречь в случае серийного, относительно стабильного производства. Однако при позаказном производстве, а также в условиях жесткой конкуренции алгоритм планирования MRP II начинает давать неудовлетворительные результаты по срокам выполнения заказа и по точности соблюдения сроков.
Алгоритм расчета APS лишен этих недостатков, так как за один раз рассчитывает необходимые закупки и производство, учитывая существующие (ограниченные) мощности и выполняемые производственные задания. Кроме того, благодаря использованию иной математической модели расчет планов производится намного быстрее — он занимает всего несколько минут (в отличие от нескольких часов при использовании стандартных систем MRP II).
Вторая часть метода APS, связанная с диспетчеризацией, реализуется с учетом всех критических мест производства. При этом APS- системы обычно позволяют накладывать и учитывать ограничения на процессы оперативного управления производством. Например, совмещение производственных партий осуществляется из расчета сбора оптимальной для запуска партии, при составлении последовательности выполнения производственных заданий производится оптимизация подготовки оборудования.
Таблица. Сравнительные характеристики методов производственного планирования.
Достоинства метода APS включают возможность получения реальных планов на основе моделирования производственного процесса и оценки различных вариантов по схеме «что-если». Кроме того, использование этого метода (и соответствующей информационной системы) позволяет в режиме реального времени, скажем, в ходе телефонного разговора, рассчитывать дату выполнения заказов клиентов с учетом сиюминутной ситуации на предприятии.
Недостатки метода очевидны. Во-первых, для его применения требуется наличие мощной ERP-системы, в которой поддерживаются функции синхронного планирования, причем тесно интегрированные с остальными модулями КИС. Во-вторых, существенно повышаются требования к точности исходной информации.
Источник